Engineering Tools Applications
Long and intricate suppliers and the criticality of tracing every component in this long chain makes permanent marking a crucial necessity of the engineering tools industry. The industry is vulnerable to disasters and uses multiple metal surfaces from stainless steel to aluminium to titanium requiring precision marking techniques to trace components. Laser marking is key to the engineering tools industry as the parts meet highest standards of quality and safety and the marking should be readable to the human eye as well as scanners.
Surfaces For Marking
Day and night markings on avionic panels |micro and major electrical, mechanical and electronic constituents | Chips, circuit boards and other navigation devices | wings and blades | thrusters and actuators | branding and bar coding on exteriors
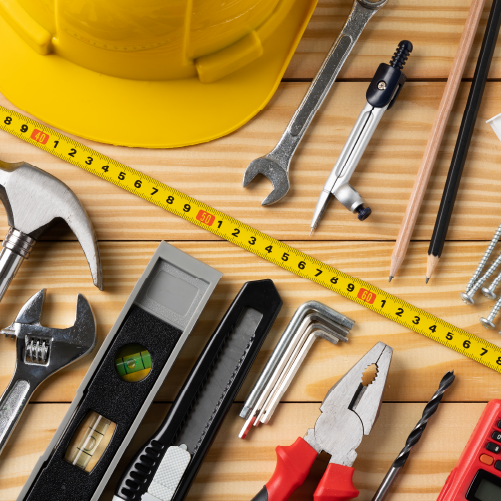
In the field of engineering tools, both dot peen marking machine and laser marking machines are widely used for part identification, traceability, and quality control. These technologies offer distinct advantages, and the choice between them depends on factors such as material properties, precision requirements, and the desired characteristics of the markings. Here’s an overview of how dot peen and laser marking machines are commonly used in the manufacturing and identification of engineering tools:
### Dot Peen Marking:
- Marking Process:
– Dot peen marking involves using a stylus to create a series of small, closely spaced dots on the surface of a material, forming alphanumeric characters, logos, or other symbols.
- Materials:
– Dot peen is suitable for marking a variety of engineering tool materials, including metals, alloys, and some plastics.
- Applications:
– Tool identification and part numbering.
– Serial numbers for traceability.
– Date codes, lot numbers, and other alphanumeric markings.
– Compliance with industry standards and regulations.
- Advantages:
– Durable and indelible markings.
– Well-suited for harsh environments and tools subjected to wear.
– Cost-effective for certain applications.
– Compliance with industry-specific marking requirements.
### Laser Marking:
- Marking Process:
– Laser marking involves using a laser beam to modify the surface of a material, creating high-contrast and permanent marks without physical contact.
- Materials:
– Laser marking is versatile and can be applied to a wide range of engineering tool materials, including metals, plastics, ceramics, and coated surfaces.
- Applications:
– 2D matrix codes for part tracking.
– Fine and detailed markings for branding and logos.
– Component serialization for traceability.
– Compliance with industry standards and regulations.
- Advantages:
– High precision and fine detail.
– Non-contact process, reducing wear on equipment.
– Flexibility in terms of design and customization.
– Suitable for applications in controlled environments.
### Integration in Engineering Tool Manufacturing:
- Quality Control:
– Both dot peen and laser marking technologies play a crucial role in quality control by providing permanent and reliable markings on engineering tools.
- Traceability:
– The ability to trace tools throughout their lifecycle is essential for maintenance, calibration, and ensuring product reliability.
- Compliance with Standards:
– Markings help ensure that engineering tools meet industry-specific standards and regulatory requirements.
- Branding and Customization:
– Laser marking is often preferred for adding branding, logos, and other customized markings with high precision.
- Durability in Harsh Conditions:
– Both technologies are chosen for their ability to provide durable markings that can withstand harsh conditions often encountered in engineering tool applications.
In summary, dot peen and laser marking machines are integral to the engineering tool industry, providing solutions for part identification, traceability, and compliance with industry standards. The selection of the appropriate technology depends on specific tool requirements, precision needs, and the environmental conditions in which the marked tools will be used.